Causes and treatment methods of motor vibration
Causes and treatment methods of motor
vibration
In industrial
production, motors play a crucial role in equipment, providing power for the
operation of production equipment. However, in the process of use and testing,
the motor will also have some abnormal conditions, especially severe vibration,
which will not only damage the equipment, but also greatly increase energy
consumption. So what are the reasons for the abnormal vibration of the motor?
Causes of motor vibration
1. Unbalanced
rotors, couplings and transmission wheels (brake wheels) can cause motor
vibration.
2. Loose iron
core support, failure of oblique keys and oblique pins, and weak binding of the
rotor will also cause imbalance in the rotating part.
3. The shaft
system of the linkage part is misaligned, the center lines do not coincide, and
the alignment is incorrect. Failure problems are mainly caused by improper
centering and installation during installation.
4. In the cold
state, the center lines of the linkage parts coincide. However, after running
for a period of time, due to the deformation of the rotor fulcrum and
foundation, the center lines are damaged and vibrate.
5. The gears
and couplings connected to the motor are faulty, the gears are badly occluded,
the teeth are severely worn, the gears are poorly lubricated, the couplings are
skewed and misaligned, the tooth shape and pitch of the gear couplings are
incorrect, the gap is too large or the wear is serious All will cause certain
vibrations.
6. Structural
defects of the motor itself, such as elliptical journal, shaft bending, too
large or too small gap between the shaft and the bearing bush, insufficient
rigidity of the bearing seat, foundation plate, part of the foundation and even
the entire motor installation foundation.
7.
Installation problems, such as the motor and the base plate are not firmly
fixed, the anchor bolts are loose, the bearing seat and the base plate are
loose, etc.
8. If the gap
between the shaft and the bearing bush is too large or too small, it will not
only cause vibration, but also cause abnormal lubrication of the bearing bush
and increase in temperature.
9. The load
driven by the motor conducts vibration, such as the vibration of the fan or
water pump driven by the motor, causing the motor to vibrate.
10. The stator
wiring of the AC motor is wrong, the rotor winding of the wound asynchronous
motor is short-circuited, the excitation winding of the synchronous motor is
short-circuited between turns, the excitation coil of the synchronous motor is
connected incorrectly, the rotor bar of the cage-type asynchronous motor is
broken, and the deformation of the rotor core causes the stator and rotor gas.
The gap is uneven, causing the air gap magnetic flux to be unbalanced and
vibrate.
Solution for
motor vibration
01. The
clearance between the tiles or bearings is too large
If the gap
between the tiles is too large, it can be adjusted by reducing the gasket at
the tile mouth to keep the gap at the top of the tiles at about one thousandth
of the shaft diameter. If there is a gap between the upper tile cover and the
tile back at this time, you can add gaskets to tighten it. If the bearing
clearance is too large, it can be solved by replacing the bearings.
02. The two
ends of the shaft are not concentric
First measure
whether the bearing seats at both ends are coaxial and adjust to the same axis.
If the shaft is not concentric, it must be machined to ensure concentricity.
03.
Insufficient shaft stiffness or unbalanced rotor
If the
stiffness of the shaft is found to be insufficient, the shaft should be
processed using high-strength materials and replaced to increase the stiffness
of the motor shaft. If the rotor is unbalanced, it must be adjusted on a
dynamic balancing machine to achieve the level of balancing accuracy.
04. Vibration
caused by vibration of working machines
The vibration
of the working machine is often transmitted to the motor, so it is necessary to
find out the cause and eliminate its impact on the motor. For example, when the
fan is unbalanced, vibration will be transmitted to the motor through the
coupling.
05. Poor
coupling alignment
The working
machine is connected to the motor through a coupling. If the alignment is not
good, axial vibration will occur. At this time, the pin should be removed, the
coupling should be aligned, and the gauge should be set to make the radial
runout, end face runout and clearance meet the standard requirements to reduce
vibration.
06. The motor
base is loose or insufficiently rigid.
When the motor
anchor bolts are loose, the vibration damping capacity decreases and the motor
vibration increases. Just tighten them. Sometimes because the base is uneven,
blindly tightening will deform the motor, changing the running accuracy of the
motor and causing vibration, which can be solved by adding shims to adjust. If
the base is not rigid enough, you can increase the rigidity of the base by
adding reinforcement or replacing the base.
07. The air
gap of the motor is uneven
When
reinstalling, the air gap of the motor should be adjusted. However, after
running, the air gap of the motor will be uneven due to vibration, looseness,
discomfort of the stopper and other reasons. At this time, the air gap must be
adjusted so that the error is less than 5%.
08. Axial
center deviation of stator and rotor
When the axes
of the rotor and the stator do not coincide, the changing magnetic field will
pull the stator to move back and forth, resulting in axial vibration. At this
time, you need to cut the coupling, start the motor, wait until it is stable,
then determine the position of the coupling, and then align it according to
this position to solve the resulting vibration.
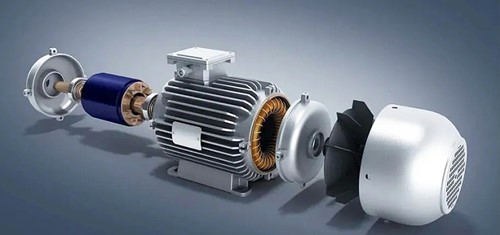