How does electric motor drive the vehicle?
The engine of most fuel vehicles generates heat (explosion) by
igniting gasoline in the cylinder, which pushes the piston to move up and down
in four strokes, and converts it into rotational motion through the crank
connecting rod, forming the power to drive the car. In other words, the engine,
like the ancient steam engine, converts heat energy into mechanical energy.
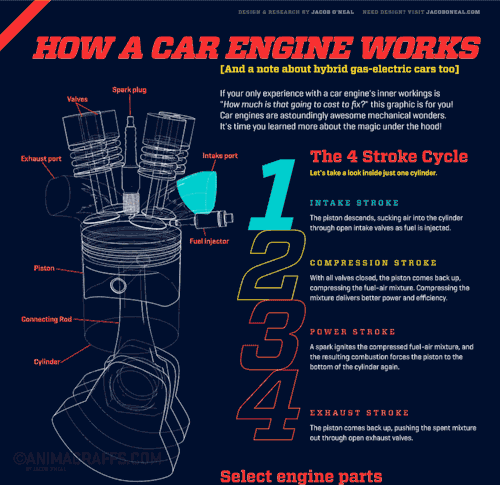
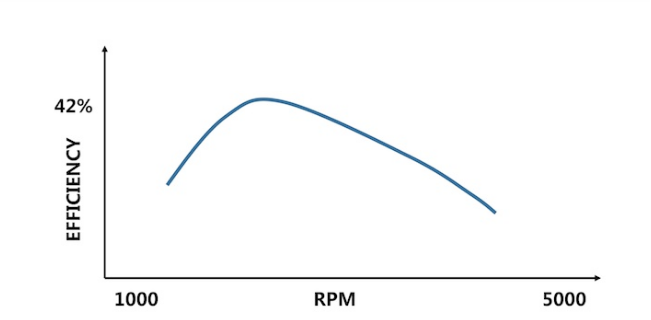
The relationship between fuel engine working speed (RPM) and efficiency
(EFFICIENCY)
The engine can only produce usable torque and power within a
limited speed range. In other words, if the car has only one gear (only the
first gear with manual transmission), then no matter how you step on the
accelerator and make the engine spin wildly, after the car reaches a certain
speed (generally no more than 20km/h), it will not speed up anymore.
This brings a lot of follow-up troubles:
1. The engine must be kept within the optimal speed range;
2. Therefore, a transmission device must be equipped to adjust
the power output by the engine;
3. The engine has a very low energy efficiency (less than 42%)
On the other hand, looking at the "motor" of the
"electric car", everything seems simple, because:
1. We don't need to worry the engine is wasting energy
when it converts the up and down movement into rotating movement. Because the
rotor of the motor is originally rotating;
2. We no longer worry about energy efficiency. Because the
motor can maintain about 90% energy efficiency at any speed;
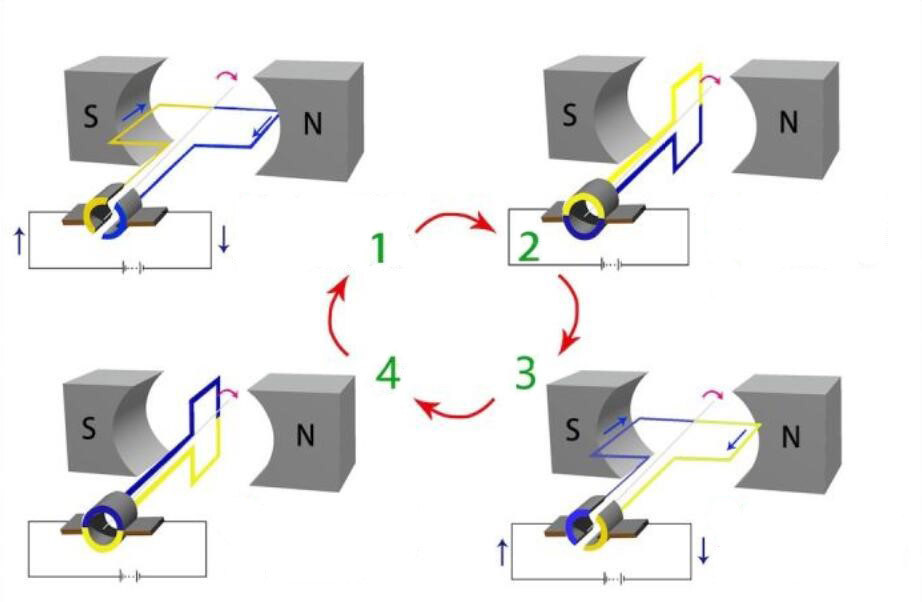
Schematic diagram of motor principle:
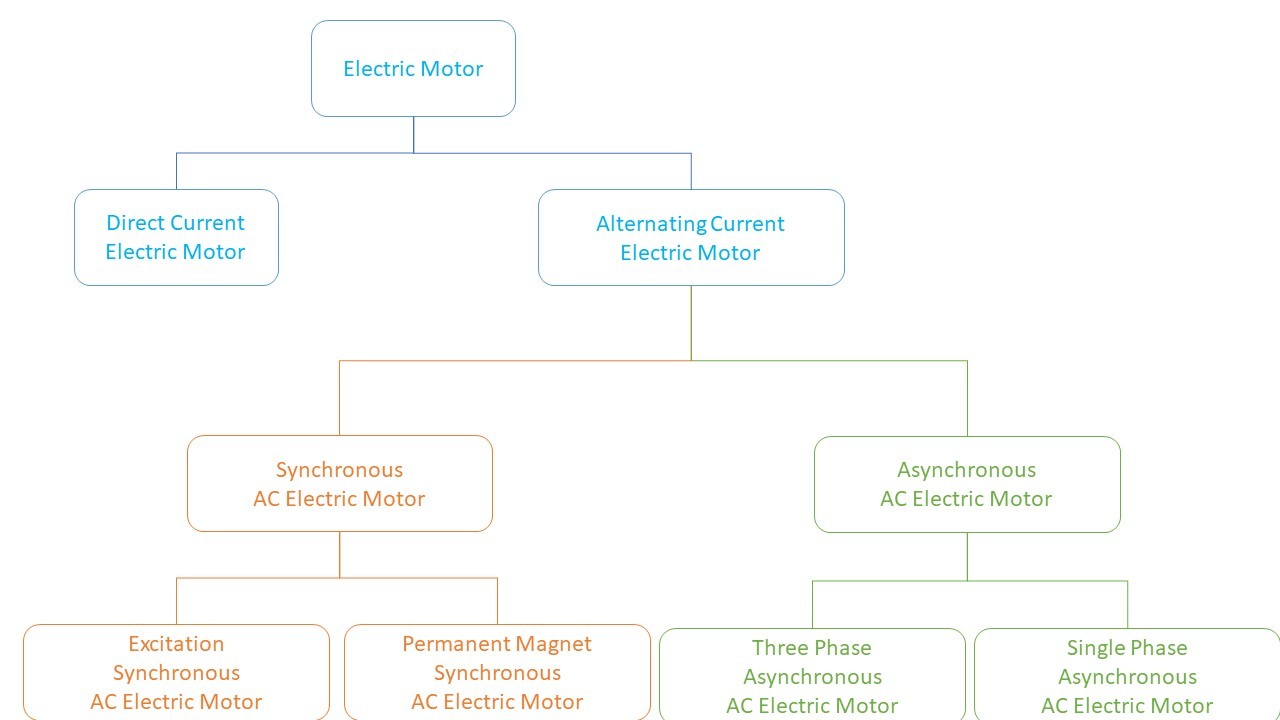
There are many kinds of electric motors, in this article we are talking about that used as traction motor for electric vehicles. First, according to different working power sources, motors can be divided into two categories: DC motors and AC motors.
AC motors can be divided into two categories: synchronous AC motors and asynchronous AC motors according to whether the rotor and stator magnetic fields are the same. Synchronous AC motors can be divided into permanent magnet synchronous AC motors and excitation synchronous AC motors; asynchronous AC motors are divided into three-phase asynchronous AC motors and single-phase asynchronous AC motors.
Most of the current household electric vehicles use AC motors, and are mainly composed of three-phase asynchronous AC motors and permanent magnet synchronous AC motors.
Basic composition of AC motor:
There are two main components: stator and rotor.
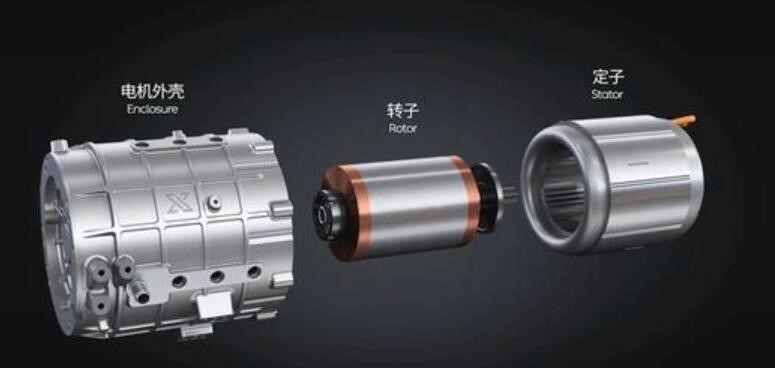
Rotor: Inside the stator is the rotor, which is either a
cylinder with many wires wrapped around it (i.e. a wound rotor), or a cylinder
with a cage structure (i.e. a cage rotor, as shown above). Because the rotor is
not fixed, but is connected to the power output shaft to rotate, it is also
called the rotor.
Rotor and stator: There are no connection or contact between the
two (this gap is called an air gap, usually 0.2~1mm), and they are sheathed in
a sleeve structure. When the stator winding is connected to AC power, the rotor
will rotate and output power.
The working principle of the asynchronous AC motor is simply:
the energized winding rotates in the rotating magnetic field. Take the
asynchronous AC motor (i.e., asynchronous induction motor) that is also used by
Tesla Motors as an example.
The stator and the rotor in the motor are not in contact. Why
does the rotor rotate when the stator winding is energized? asynchronous motor working principle:
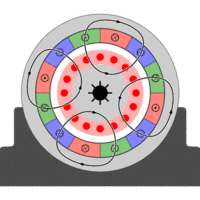
Asynchronous motor working principle GIF
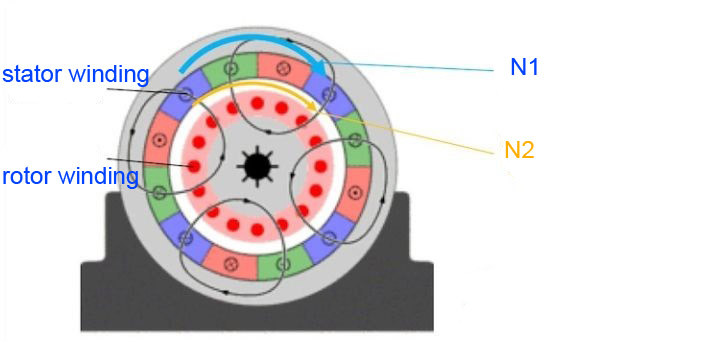
Magnetic field rotation speed of stator magnetic field rotation direction: N1
Rotor rotation speed: N2
N1>N2
N1=N2 Synchronous AC Electric Motor
Throughout the work process, we will find an interesting
phenomenon: because the stator needs to be energized to generate a rotating
magnetic field, this magnetic field causes the rotor to rotate by
electromagnetic induction, so the rotor speed is not synchronized with the
stator magnetic field speed (the speed difference is about 2%~5%). Therefore,
we call it an asynchronous AC motor. Conversely, if the two speeds are the
same, we call it a synchronous AC motor.
The most widely used asynchronous AC motors in the industrial
field are three-phase asynchronous AC motors. In the field of electric
vehicles, Tesla Motors and NIO Motors are representative of using such motors.
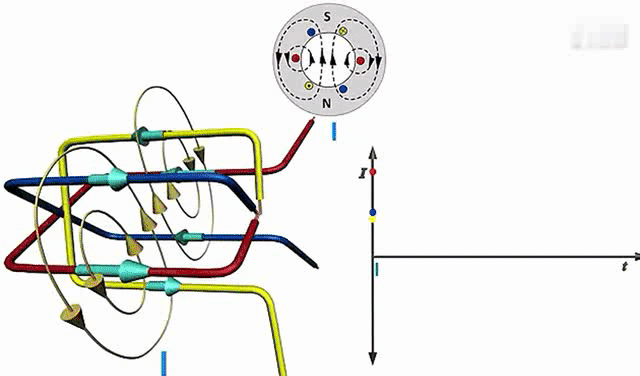
The working principle of three-phase asynchronous
AC motor
The special feature of the three-phase asynchronous AC motor is that the stator winding is a symmetrical three-phase winding in space. As shown in the figure above, the position of each phase in space differs by 120° from each other. When the three-phase windings are connected in a star shape and the alternating current is connected, then three symmetrical currents (three-phase currents) are generated in the stator.
The influence of the internal stator magnetic field of a
three-phase AC motor on the rotor:
The rotating magnetic field vector formed by the three-phase
current will superimpose and affect the rotor, so that the rotor can rotate
faster (compared to the single-phase asynchronous AC motor), and its speed can
reach 12000~15000r/min, thereby driving electric vehicles.
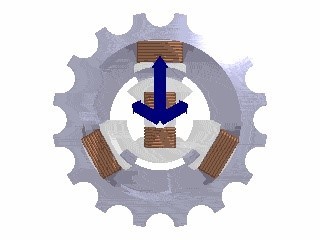
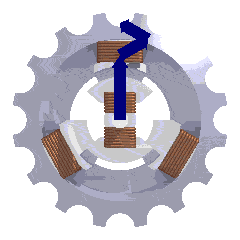
Features of AC motors:
Let me talk about its advantages first, we can see from the
above structure and working principle introduction:
1. The structure is simple, the weight is relatively light, and
the volume is relatively small;
2. Reliable operation and durable;
3. The motor body has low manufacturing cost and easy
maintenance.
The common structure of a synchronous motor:
Earlier, we mentioned that in an asynchronous AC motor, under
the action of Lenz's law, the rotor follows the rotating magnetic field of the
stator to rotate, which causes the two speeds to be asynchronous, so it is
called an asynchronous motor.
However, if the current in the rotor winding is not induced by
the stator rotating magnetic field, but generated by itself, that is, the rotor
magnetic field has nothing to do with the stator rotating magnetic field, and
its magnetic pole direction is fixed, then according to the principle of same
sex repulsion and opposite sex attraction, The rotating magnetic field of the
stator will pull the rotor to rotate, and make the rotor magnetic field and the
rotor and the stator rotating magnetic field rotate synchronously. This is the
basic working idea of a synchronous motor.
Common structure and principle of permanent magnet
synchronous motor:
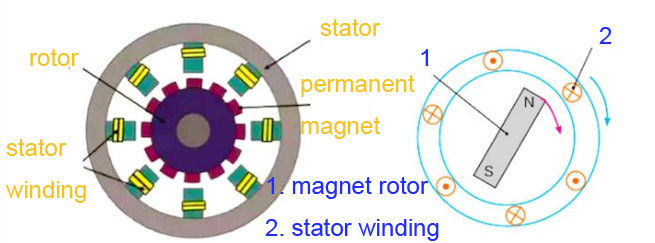
Compared with asynchronous motors, because the rotor has its own
magnetism, when the stator windings are energized, the rotor is immediately
stressed, which makes the stator magnetic field and the rotor speed
synchronized.
Features of permanent magnet synchronous motor
It has a higher power-to-mass ratio, smaller size, lighter
weight, greater output torque than other types of motors, and its limit speed
and braking performance are also excellent. Therefore, permanent magnet
synchronous motors have become current electric vehicle applications the most
electric motors.
However, the performance of permanent magnet motors is closely
related to permanent magnet materials. The permanent magnet materials currently
used in permanent magnet motors include ferrite, aluminum nickel diamond,
samarium cobalt, neodymium iron boron and so on.
1. Ferrite: low price, linear demagnetization characteristics,
it is a commonly used permanent magnet material. Ferrite has a low magnetic
energy product, and a motor made of ferrite has a larger volume.
2. AlNiCo: The material has high remanence, but low
coercivity, low demagnetization resistance, short life, and is less used in
motors.
3. Samarium cobalt: The material has high remanence and
coercivity. The only drawback is that there are not many resources and
expensive, which limits the application.
4. Neodymium iron boron: The material has high remanence,
coercivity, magnetic energy product and relatively low price. It is currently
the most suitable permanent magnet material.
China has abundant NdFeB materials-rare earth metals. The rare earth permanent magnet material has excellent magnetic properties. After magnetization, it does not require additional energy to establish a strong permanent magnetic field. The rare earth permanent magnet motor used to replace traditional motors is not only efficient, but also simple in structure, reliable in operation, and bulky. Small and light.
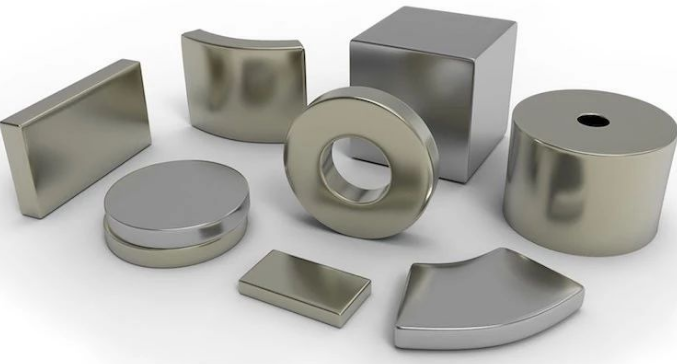
In addition, the properties of permanent magnet materials are usually related to temperature. If the temperature of the magnet increases, the rate of loss of remanence will increase. If the temperature of the permanent magnet exceeds the Curie temperature, it will completely lose its magnetism (magnetism is zero). The demagnetization characteristic curve changes with temperature, and within a certain temperature range, its change is reversible and approximately linear.
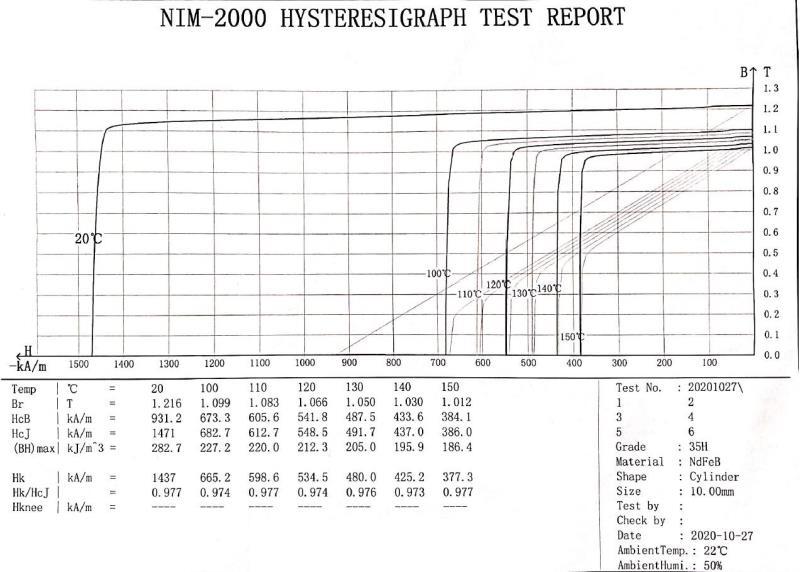