Will AC asynchronous motors be replaced by permanent magnet synchronous motors in EV?
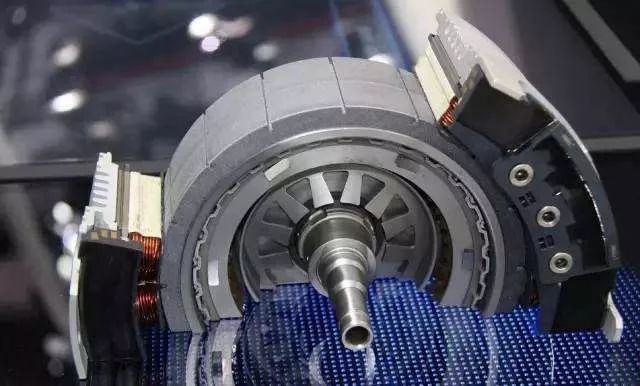
Permanent magnet synchronous motor
Different types of electric motors were introduced earlier. Compares to asynchronous ac motor, PMSM(permanent magnet synchronous motors) has
advantages as below:
1, The
magnetic field of the permanent magnet synchronous motor is generated by
permanent magnets, the excitation loss caused by the magnetic field generated is avoided.
2,
The external
characteristic efficiency curve of the permanent magnet synchronous motor has a
higher efficiency value at light load. Compared with the asynchronous motor,
this is the biggest advantage of the permanent magnet synchronous motor in
terms of energy saving.
3,
Due to the high-power
factor of the permanent magnet synchronous motor, its current is smaller than
that of the asynchronous motor. Therefore, the stator copper loss of the motor
is small and the efficiency is high.
4,
Transmission
system is highly efficient. The parameters of the permanent magnet motor,
especially the power factor, are not affected by the number of motor poles, so
it is easy to design a multi-pole motor, so that the traditional load motor
that needs to be driven by the gearbox can be turned into a permanent magnet
synchronous motor, and a direct drive system driven by the motor The gearbox is
omitted and the transmission efficiency is improved.
1. High power
factor, low motor current, reduce copper consumption of motor stator, more
energy saving
2. The power
factor is high, the power capacity of the motor can be reduced, and other
auxiliary facilities such as switches and cables can be smaller, and the
corresponding cost is lower
3. The power
factor of the permanent magnet synchronous motor is not affected by the number
of poles of the motor. If the motor support system allows, the number of poles
of the motor can be designed to be more, the corresponding motor volume is
smaller, and the direct material cost of the motor is lower.
Simple and Flexible Structure
Due to parameters of the permanent magnet
synchronous motor are not affected by the number of poles of the motor, it is
convenient to realize the direct drive of the load by the motor, and the
gearbox with high noise and high failure rate is eliminated.
The permanent magnet is in rotor in traditional permanent magnet motor, leading to a low structural strength of the rotor, and the heat generated by the permanent magnet is difficult to dissipate, which restricts the ability of the motor to output mechanical energy.
The traditional permanent magnet motor drive system has two disadvantages.
First, the speed range is narrow, which means it is difficult to ensure good performance and high efficiency at low speed and high speed.
Second, fault tolerance is poor, that is, when a fault occurs, it
is difficult to maintain the motor to continue to work.
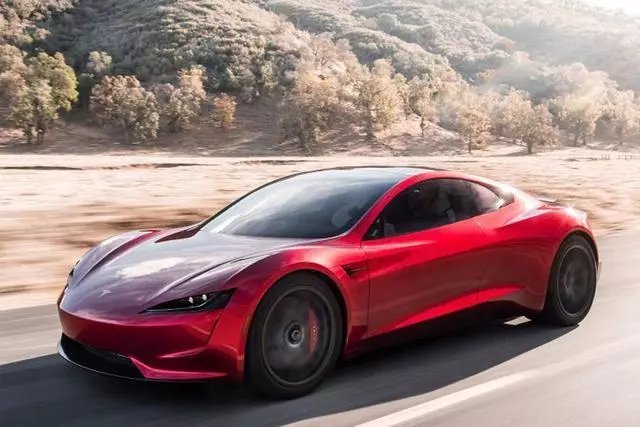
In EVs, most domestic
manufacturers prefer permanent magnet synchronous motors, but most
European and American companies choose AC induction motors. This is
mainly due to the following reasons:
1. The electric
cars of European and American manufacturers were originally mainly electric
sports cars, which required larger torque to achieve high acceleration. With
the advancement of technology, although permanent magnet synchronous motors
have appeared and are more efficient, It is obviously impossible for European
and American manufacturers to abandon the mature induction motor technology and
turn to the research and development of induction synchronous motors. The
reason why domestic manufacturers adopt more permanent magnet synchronous
motors is also related to market environment factors. The most iconic is Telsa and BMW I3.
2. Leaving aside market and technical factors, the rare earth materials currently used in permanent magnet synchronous motors are relatively rare overseas. According to data, China currently has about 70% of the world’s rare earth resources, and the main raw material of permanent magnets is made of neodymium iron boron magnetic materials. The total output has reached 80% of the world's total. Under such an environment, it would not be surprising that China is dominated by permanent magnet synchronous motors.
Chery, Weimar, etc., and there are many PMSM manufacturers, including Siemens, Bosch, Continental etc. BAIC New Energy and BYD
have also developed their own permanent magnet synchronous motors.
Induction motors require more efficient and
complex cooling systems than permanent magnet motors.
Although the coil structure of the motor is not
like permanent magnets, it is easy to demagnetize at high temperatures, but
because of the extra part of the energized coil, the rotor part of the
induction motor heats up at the same speed and power output. It's also faster.
The power loss of the permanent magnet rotor is about one-tenth or less of that
of the induction motor coil rotor, and the power loss of the coil rotor up to
ten times is mostly used for resistance heating, so the induction motor rotor
needs a more efficient cooling circuit. A higher power cooling circuit means a
higher cost oil and water-cooling system, which is only a disadvantage. For
more efficient cooling, most of the rotor coils are cooled by direct injection
of oil, and the cooling oil is often shared with other mechanical structures:
such as bearings and motor gearboxes. If the motor heats up too fast, the oil
will not have time to cool or the oil temperature will continue to be
relatively high, which will directly affect the cooling and lubricating effect
of other mechanical structures. This is the effect of motor heating on the
cooling of the entire traditional system, which is a system-level problem.
Therefore, the limited torque output of the induction motor due to overheating
is not necessarily the occasional peak power output, but it is more dangerous
when the long-term high-power output = long-term high-power heat release.
ES6 utilize permanent magnet motor which is 160kw in the front and 240kw asynchronous motor in the back. This
asynchronous motor is not always working, it only starts to work when the
computer detects that you have the will to accelerate. Therefore, the energy
consumption is not particularly high. This collocation avoids the contradiction
of mutual repulsion between dual permanent magnet motors and the bottom battery
of the rear box, extends the cruising range, and considers high performance.
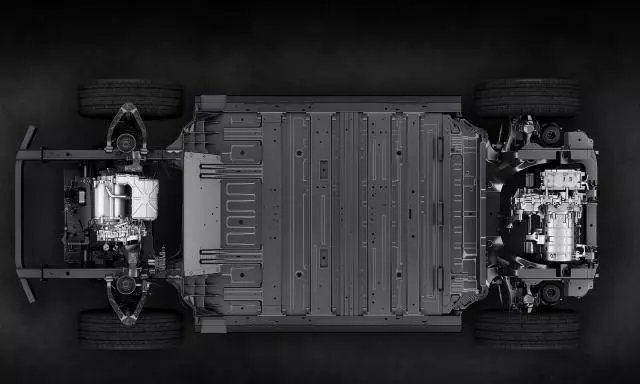