Passivation one common surface treatment of magnets
We all know that the sintered NdFeB permanent magnet material is
produced by powder metallurgy technology. It is a kind of material with
relatively active chemical properties. There are tiny pores inside, and the
Nd-rich phase is easy to oxidize in the air. After the material is corroded or
damaged by the components, the magnetic properties will be attenuated or even
lost over time, which will affect the performance and life of the whole
machine, so strict anti-corrosion treatment must be carried out before use.
The surface protection of NdFeB permanent magnets has three
aspects:
1-Improve the corrosion resistance of NdFeB, and use various
surface protections to resist corrosion such as humid environments, acids,
alkalis, salts, and harmful gases;
2- Thoroughly clean the surface of the magnet, such as removing
the loose magnetic particles on the surface, to form a smooth surface to
prevent the loose magnetic particles from affecting the function or damaging
the magnetic system;
3-Operation protection, prevent magnetic particles from falling
off during assembly or work.
NdFeB passivation is like phosphating, which is to form a
protective film on the surface of the workpiece through a chemical method on
the neodymium iron boron surface to achieve the purpose of anti-corrosion of
the workpiece. Surface chemical conversion coating technology is a common
method of surface treatment. At present, NdFeB surface chemical conversion
coating treatment mainly uses phosphating technology, mostly ordinary zinc, or
iron phosphating. The phosphating film itself has poor corrosion resistance and
often It does not independently undertake the anti-corrosion effect, but
cooperates with electrophoresis, coating, etc. as the outer layer of composite
anti-corrosion. At the same time, phosphoric acid and phosphate compounds are
used in a large amount in the phosphating process, which is prone to phosphorus
pollution, causing adverse consequences such as eutrophication of water bodies.
The process environment is not friendly. Compared with the phosphating agent,
the passivating agent has simple components, does not contain phosphoric acid
and phosphate compounds, and is more environmentally friendly.
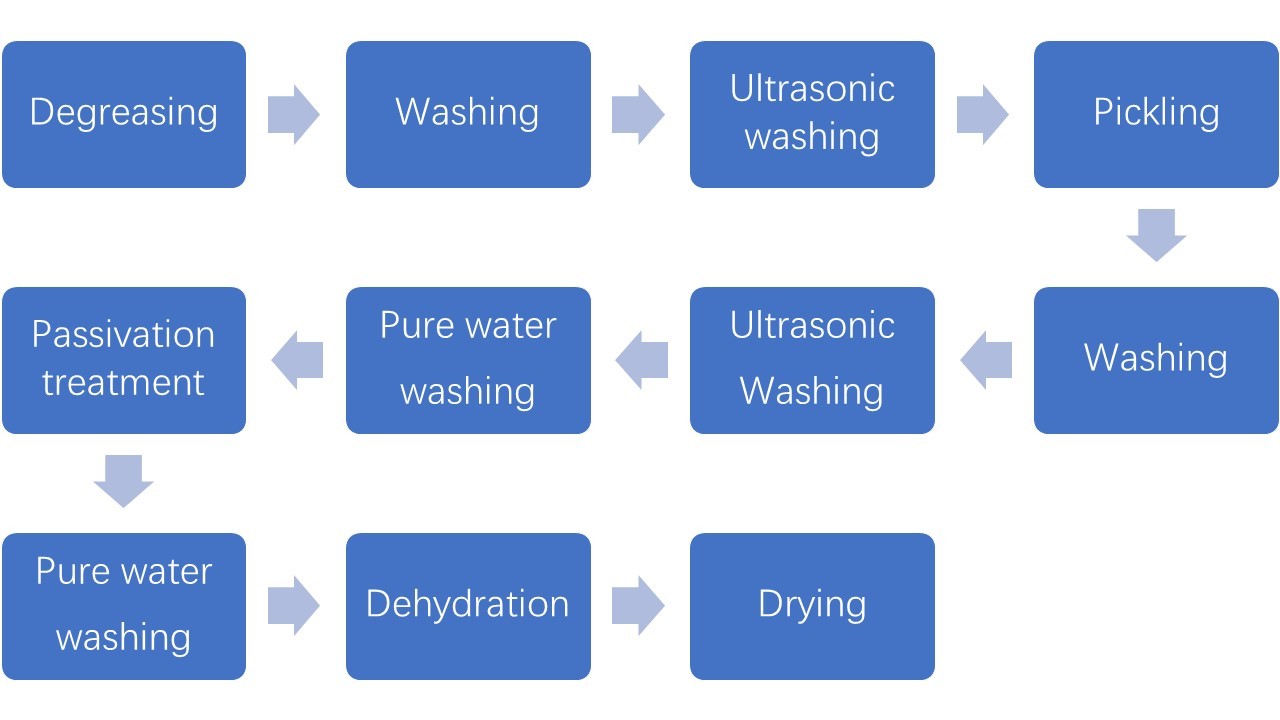
Degreasing
Degreasing can only remove grease, dust, sweat stains and
attached metal shavings on the surface of the NdFeB, but not the rust on the
magnet. The oil stains on the surface of NdFeB are brought from the processing
of materials, such as anti-rust grease used to prevent rust during storage and
transportation, and cutting fluid that parts meet during cutting.
Before further surface treatment of NdFeB, the oil on the
surface must be cleaned, otherwise it will affect the quality of surface
chemical conversion, electroplating or coating. Due to the wide range of
sources and types of oil pollution, the degree of pollution varies greatly, so
the problem of oil removal is very complicated. In order not to cause corrosion
and subsequent residue in the degreasing process, try to use a degreasing agent
with low free alkalinity and total alkalinity.
Pickling
The purpose of pickling is to remove the black ash and rust left
on the surface of the neodymium iron boron. Pickling liquid generally uses
2%~4% nitric acid, and the time is 0.5~2.0 min. Both high acid concentration
and long pickling time are detrimental to the magnet.
Passivation
The passivation treatment method is to place the magnet in a
container containing passivation solution, soak, or spray for a period, or use
the magnet as an anode to pass polarization to achieve passivation, that is, a
passivation film is formed on the surface. As an important surface
anti-corrosion treatment, passivation is commonly used in many metals,
especially metals such as aluminum, zinc, cadmium, tin, and magnesium and their
alloy materials.
Most of the traditional passivation treatments use chromic acid
and chromate as treatment agents, called chromate passivation. The chromate
conversion film formed on the metal surface after treatment has a good
corrosion protection effect on the base metal. . As a separate protective film,
the passivation treatment is simple and practical, and the cost is low. It was
widely used in the early development of NdFeB. But its fatal weakness is that
it contains toxic chromium Cr (Ⅵ),
which is harmful to the human body and the environment, which has prompted
people to actively carry out research on effective alternative technologies. In
recent years, my country has many patents for passivation agents. There is a
passivation agent for neodymium iron boron magnets, including: oxalic acid, surfactants,
and complexing agents. Its composition is simple, and it has the functions of
degreasing, rust removal, and passivation at the same time. Without the use of
phosphoric acid and phosphate compounds, it is a more convenient and
environmentally friendly passivation agent for NdFeB magnets.
In recent years, the corrosion resistance requirements for NdFeB
conversion coatings have become higher and higher, and it is difficult to meet
the requirements by single passivation technology. The commonly used process is
to use composite conversion coating technology, that is, phosphating and then
passivating, by filling phosphorus the pores of the chemical film can
effectively improve the corrosion resistance of the composite conversion film.