Why OEMs don't produce parts?
80% of the parts of a whole car are not produced by the OEMs. Why OEMs don't produce all the parts of a car? Is it incapable or deliberate? This issue will decipher, why most of the parts are not produced by automakers!
What does a car manufacturer produce?
Let’s talk about what auto manufacturers produce first. Most factories mainly provide design requirements for automobiles,
contact suppliers, conduct automobile reliability and safety tests, and adjust
parts that need to be adjusted. In terms of production, it mainly produces
sheet metal parts, some plastic parts, and some rubber parts, as well as
welding and painting, assembling all parts, and finally car testing. There are
very few automakers that could produce engines, transmissions, and suspension
systems.
If we look at the above, we will find that car engineering design, styling and even software calibration, engines and transmissions are all done by other companies, not to mention airbags, seats, steering wheels, air conditioning systems, and interior buttons Parts. So car manufacturers do this because they don't have the ability to do this! Or do you have your own ideas based on other considerations, let's talk about this now.
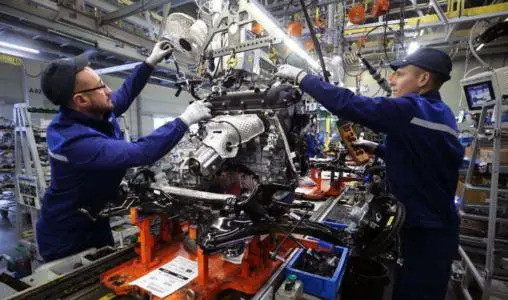
Reduce corporate capital risk
The first reason
all companies do this is for the purpose of reducing corporate capital risks.
This is also the most conducive to the health of a company’s capital. Because
it is a huge project from car design to production to the final listing. For a
company, the more links involved, the more capital invested, and the greater in overall risk. Once there is a problem in a certain link, more capital
is needed to be continuously injected to solve the problem. As a result, once
the capital chain is tight or broken, the entire industry will face great
risks.
In other words,
the longer front is drawn, the greater in risk. In order to
increase their anti-risk capabilities, current auto companies are all
relatively small and sophisticated companies. This way, no matter what kind of
events they face, their overall anti-risk capabilities are very strong, which
reduces overall capital risk of a company.
Another point is
about safety, emissions, national regulations, and even large-scale
recalls of cars due to certain problems are designed. In this case, if the
parts are produced by car manufacturers, then all the recalls will bring huge
Expenses and compensation need to be borne by automakers themselves, and
the huge recall costs caused by many major problems are very fatal to a
company. If it is supplier’s parts and components, the entire cost of the
recall will be borne by the supplier and the company. This situation will
effectively reduce the company’s capital risk.
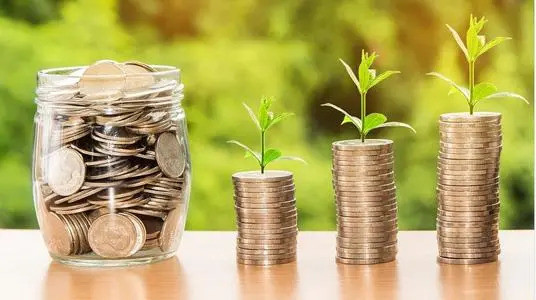
Increase work efficiency
There is another
advantage of adopting supplier and outsourcing design, that is, it can
effectively improve work efficiency. Engineers who have worked in a
automotive design industry, especially those who have worked in automotive
factories, know a term, that is, "prevarication". That means if responsibilities for a project is not clear, then most
of them will face their own heavy workload. When facing this project, engineers
will launch it. If they can’t push it out, they will also rip-off between
relevant departments and try to share part of the project.
This is a very
common phenomenon in auto factories, because it has a
relatively large work in auto industry. From an economic point of
view, this form of enterprise will have a greater internal digestion.
Therefore, if internal design and review of internal consumption of the
enterprise are used, the overall progress will be delayed due to the
disconnection of the various stages. Therefore, most auto companies adopt
outsourcing design and are only responsible for auditing, which will greatly
improve work efficiency.
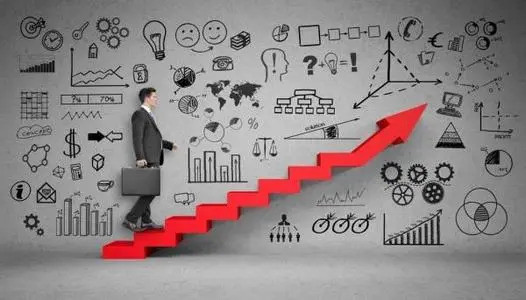
Lower cost
In terms of
production, the advantage of using suppliers is also a very important point
that can reduce costs. Seeing this, many car friends may not understand that
outsourcing will be cheaper than self-produced? The answer is yes. Because
self-production requires purchase of many productions’ equipment,
construction of factories, recruitment, management, and a series of tasks, and
because current auto companies produce more models, the use of each
component is very small.
And modern
industry has a characteristic, that is, cost will decrease as number of
overall parts increases. Simply put, if a plastic part is produced at 10,000
pieces, cost may be 0.5 yuan, and after 1 million pieces are produced, cost may become 0.1 yuan. For entire vehicle, such a cost reduction is very
objective. The supplier is specialized in the production of a certain part.
Naturally, more orders are received, and there is no need to start from scratch
for the investment in site and equipment. Therefore, supplier's supply
method will reduce the cost of production than its own production. a lot of.
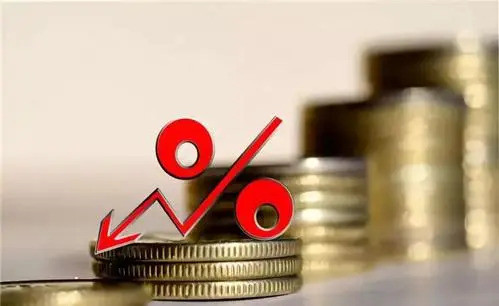
Conducive to quality control
Another
advantage of using suppliers is that it is conducive to quality control. If the
parts are produced by their own manufacturers, there is a situation that the
production department will force the design department to introduce new
equipment or change the design plan to reduce the difficulty of production.
This is naturally not conducive to quality control, and the quality control of
internal companies is also difficult to compare with the cooperation between
companies.
However, it is
easier to adopt a supplier, because you only need to make a request. If supplier cannot meet the requirements or price is too high, then you can
switch to another supplier. Moreover, the degree of overcoming difficulties by
suppliers is much better than that between enterprise departments. In addition,
the quality control of a enterprise can also be stationed in supplier’s
enterprise quality control, and regular spot checks to monitor the quality of supplier, this requires very little manpower and financial resources, so
the supplier’s supply method is compared with that. A large and complete production
is more conducive to quality control.
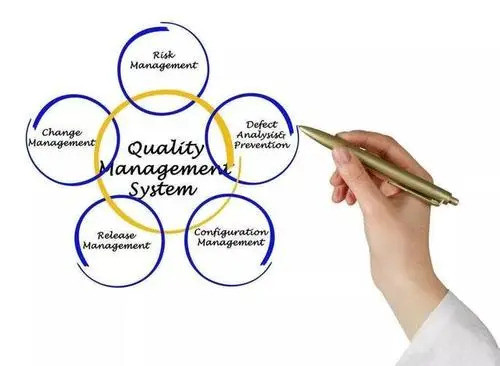
Enhance the competitiveness of automotive products
The last point
of using suppliers or design outsourcing is that it can quickly and effectively
enhance the competitiveness of automotive products. It is the most correct
choice to entrust one thing to the right talent in the right event. There is a
specialization in art industry. Regarding the upgrading and R&D of
parts, whether it is technology or materials, suppliers who specialize in one
or a few items will be much better than those who do everything in terms of the
level of technology and the speed of continuous change.
If a
manufacturer is like a supplier, it needs a huge team of engineers to research
and develop everything. Maybe the scale of a company will be dozens or even
hundreds of times, and there are no such companies in current economic
system of the world. Space, when a company develops to this scale, everything
is done by yourself, and result can only be dragged down by huge
management costs and internal friction. Therefore, it is the best choice to
leave professional matters to professional people.
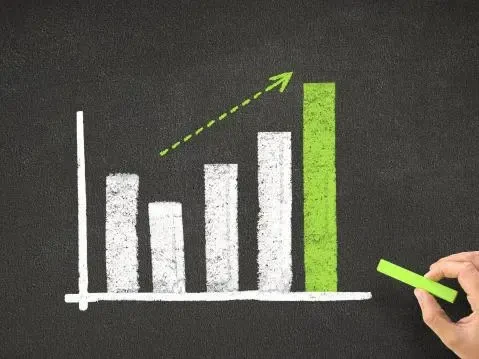
At last
The automobile
industry is a very large system, and each automobile company needs to cooperate
with integrated suppliers to complete a car. In addition to design and
assembly of manufacturer, the quality of a car has a lot to do with the
car supplier. Current car is a global product. It is very unreliable to
simply judge the reliability and overall performance of a car based on the
car series and brand. Therefore, if you want to choose a car, you need to
analyze and investigate the specific model in detail, and then go for a test
drive in person to judge whether a car is suitable for you.