Some introductions of DACROMET
There are many kinds of metal surface treatments, such as electroplating, blackening oxidation, phosphating and so on. There is a kind of surface treatment called DACROMET, which is relatively unfamiliar to everyone. Maybe you have seen this kind of surface treatment product, but you don't know that it uses DACROMET treatment process.
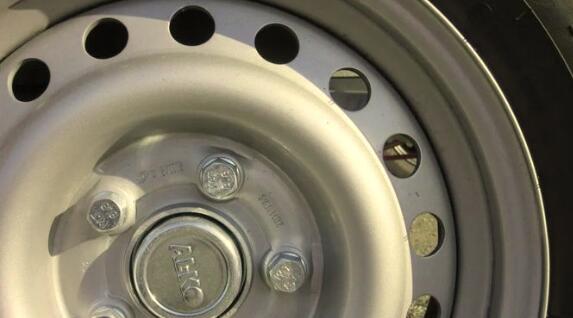
So what is the DACROMET surface
treatment process, what is the difference between this surface treatment
process and other metal surface treatment processes, and what special function
does it have?
DACROMET is a
new type of metal surface anti-corrosion coating that uses metal aluminum, zinc
and chromic acid as the main coating materials.
DACROMET 's
base materials are mainly steel and non-ferrous metals. After the coating liquid
reacts with the metal base, a silver-gray anti-corrosion film will be formed on
the surface, which can isolate the base from the air and protect the workpiece.
DACROMET is
widely used in various industries, such as construction, hardware, fasteners, road
engineering, petrochemicals, etc.
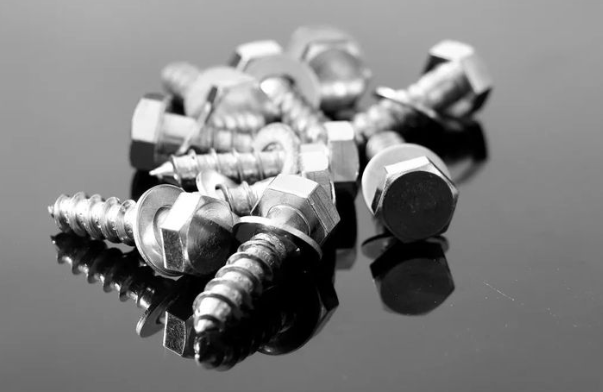
DACROMET has a very strong anti-corrosion
performance, which makes up for the shortcomings of traditional anti-corrosion
time, and pushes the anti-corrosion technology to a new level.
Features of DACROMET
Compared with some traditional electroplating
processes, DACROMET has more advantages.
For example, the anti-corrosion performance of products using
DACROMET process is dozens of times that of traditional galvanizing. After
passing the salt spray test, it is found that ordinary DACROMET can reach 20
times that of galvanizing, while those long-term DACROMET tests The time will
be longer. Some parts in the nuclear industry use DACROMET technology and the
service life can reach 30 years.
DACROMET will not crack or break after being stretched and
stressed like other electroplating processes.
DACROMET has good stability in high temperature environment,
which is much higher than traditional galvanized high temperature resistance.
The products after using the DACROMET process have very good impact
resistance, so the DACROMET process is very suitable for those stressed parts.
This is because DACROMET has good permeability and can well combine the surface
coating with the product.
Unlike some traditional electroplating processes, DACROMET has
less pollution in the production process, so some high-polluting surface
treatment processes are gradually being replaced by DACROMET.
Although DACROMET has many advantages, it also has some shortcomings.
Some DACROMET contain hexavalent chromium ions that are harmful
to the body, which will cause harm to the human body after long-term exposure
and have the risk of causing cancer. According to the relevant product
standards, it is not allowed to contain this harmful substance.
The surface color of DACROMET 's craft is only silver and white,
which is relatively single, so other colors must be post-processed again to
obtain different colors.
DACROMET coating has poor electrical conductivity, long time in
the production process and high energy consumption, which also limits its scope
of use.
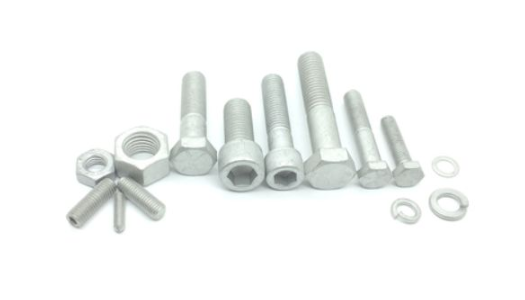
Production process of DACROMET
Degreasing and degreasing
Workpieces with grease must be degreased and degreasing on the
surface. The effect of degreasing and degreasing will directly affect the
adhesion and anti-corrosion quality of the entire coating.
Usually, the organic solvent mixed with trichloroethylene and
industrial alkali is used for degreasing and degreasing. Soak the workpiece in
the solution for half an hour to complete the degreasing. After the degreasing
is completed, remove the workpiece and rinse the surface of the workpiece with
clean water.
Polishing
There will be some burrs or rust on the surface of the
workpiece. The surface needs to be cleaned, and the workpiece is placed in a
shot blasting machine or directly polished with a machine, which can improve
the corrosion resistance of the workpiece.
Coating
The coating solution used by DACROMET is mainly composed of
aluminum, zinc, ethylene glycol and chromic acid, which are mixed and stirred
for use.
Some small or standard parts are usually immersed in liquid. Put
these workpieces in the coating solution for about ten seconds, so that the
surface of the workpiece is completely covered with the coating liquid, and
then remove the workpiece, in order to avoid liquid accumulation and sagging. ,
Use centrifugal force to remove the excess coating liquid on the workpiece.
There are also some larger workpieces that cannot be completed
by immersion. This requires the use of machinery and equipment to spray the
coating liquid on the surface of the workpiece. The surface adhesion of the
workpiece using the spray method is poor, and the corrosion resistance will
also be reduced.
Baking curing
After the liquid is coated on the surface, first bake it at
120°C for about 10 minutes. This is to slowly evaporate the water in the
coating liquid and allow the coating liquid to fully contact the workpiece.
Bake at 300°C for about 30 minutes to fully cure the coating
liquid on the surface of the workpiece, and finally form a thin film.
Post-processing
The temperature of the workpiece after baking and curing will be
very high, and the workpiece must be quickly cooled by the cooling system, and
the workpiece after the final inspection completes the entire DACROMET process.

DACROMET was born to provide
better anti-corrosion performance for automobiles. It can be said that it has
gone to the world through automobiles and improved many shortcomings such as
galvanizing processes. Therefore, it has been widely used. However, with the
development of technology, people Always looking for a better and more perfect
surface treatment process.