Several problems should be paid attention to in the pretreatment of NdFeB permanent magnet electroplating

NdFeB magnetic material is made by mixing, pressing and sintering the sieved neodymium, iron and boron ultrafine powder. According to the requirements of product use, it can be machined into different shapes. Because the chemical properties of this material are relatively active and easily oxidized, the finished product needs to be processed by electroplating. However, the quality of electroplating coating is closely related to its pretreatment. This pretreatment process generally includes degreasing, rust removal, activation and other processes. If one part of this pre-treatment process is not handled cleanly, it will bring latent defects to the final electroplating product, resulting in problems such as blistering and peeling of the electroplating layer. Defective magnetic material parts lose their marketable value and are scrapped. If magnetic material parts with hidden defects are applied to the equipment, the whole machine may fail due to the failure of such unqualified parts. even serious consequences.
NdFeB magnetic materials are not as dense as wrought metal materials. It is a microporous material. Its porosity brings many difficulties and troubles to the electroplating pretreatment. In addition to removing the alkaline and acidic substances on the surface of the workpiece and the dirt brought in by the machining process, the biggest difficulty is how to remove the dirt in the micropores.
For low-grade magnetic materials with low general requirements, the pre-treatment processes used in the past are: alkaline degreasing - water washing - pickling (bleaching, neutralization) - water washing - surface activation - electroplating. Although this process is simple, it has higher requirements on degreasers, and needs to use Nd-Fe-Boron special degreaser. The formula of this degreaser is complicated and requires many kinds of raw materials. trouble. And once the ratio is improper, it will fail and the practicability is poor.
Since the advent of high-power ultrasonic cleaners in industrial production, this problem has been solved. The unique cavitation effect of ultrasonic cleaning can completely remove the alkaline and acidic substances remaining in the micropores of the magnetic material.
After ultrasonic cleaning, the pretreatment process of neodymium-iron-boron magnetic materials is generally as follows:
(1) Alkaline degreasing - water bleaching - water bleaching - ultrasonic fine bleaching - dilute nitric acid treatment (neutralization, bleaching) - water rinsing - water rinsing - ultrasonic fine bleaching - activation treatment - electroplating
(2) Alkaline degreasing - water rinsing - water rinsing - ultrasonic fine bleaching - dilute nitric acid (neutralization, bleaching) treatment - water rinsing - water rinsing - ultrasonic fine rinsing - activation treatment - water rinsing - water rinsing - ultrasonic fine rinsing - plating
(3) Ultrasonic alkaline degreasing - water rinsing - water rinsing - ultrasonic fine bleaching - dilute nitric acid (neutralization, bleaching) treatment - water rinsing - water rinsing - ultrasonic fine rinsing - activation treatment - water rinsing - water rinsing - ultrasonic fine rinsing -plating
The choice of cleaning method
The placement of the workpiece in the cleaning tank has a great relationship with the cleaning quality, and its placement is also related to the size, shape and structure of the workpiece. Generally speaking, overlapping stacking between workpieces, or stacking too much at one time will affect the cleaning effect.
Although neodymium-iron-boron magnetic materials have different shapes, they are mostly small parts. It can be placed on a nylon mesh and shaken and cleaned in the cleaning tank, which will help the dirt on the surface of the workpiece to fall off, and it is also conducive to the destruction of the water film of the workpiece with blind holes, so that the cavitation effect is easy to occur in the blind holes. Another placement method is to directly flatten the workpiece on the bottom plate of the cleaning tank (that is, the ultrasonic transducer radiation plate), so that the workpiece can be subjected to strong ultrasonic impact. Practice has proved that this method of cleaning the workpiece directly on the bottom plate has the best cleaning effect and the highest efficiency.
The choice of power density
It is well known that cavitation can only occur when the ultrasonic output reaches a certain intensity. Generally, the lowest power density in water should be greater than 0.3W/cm2. However, if the power density is too large and the cleaning ability is improved, it may cause mechanical damage or cavitation corrosion on the surface of the workpiece. If the power density is too small, the production efficiency is too low, and even the cleaning quality of the workpiece cannot meet the requirements. Generally, the ultrasonic cleaning machine used in the machining industry has a surface power density of 0.40-0.8W/cm2 and a bulk power density of about 25W/L.
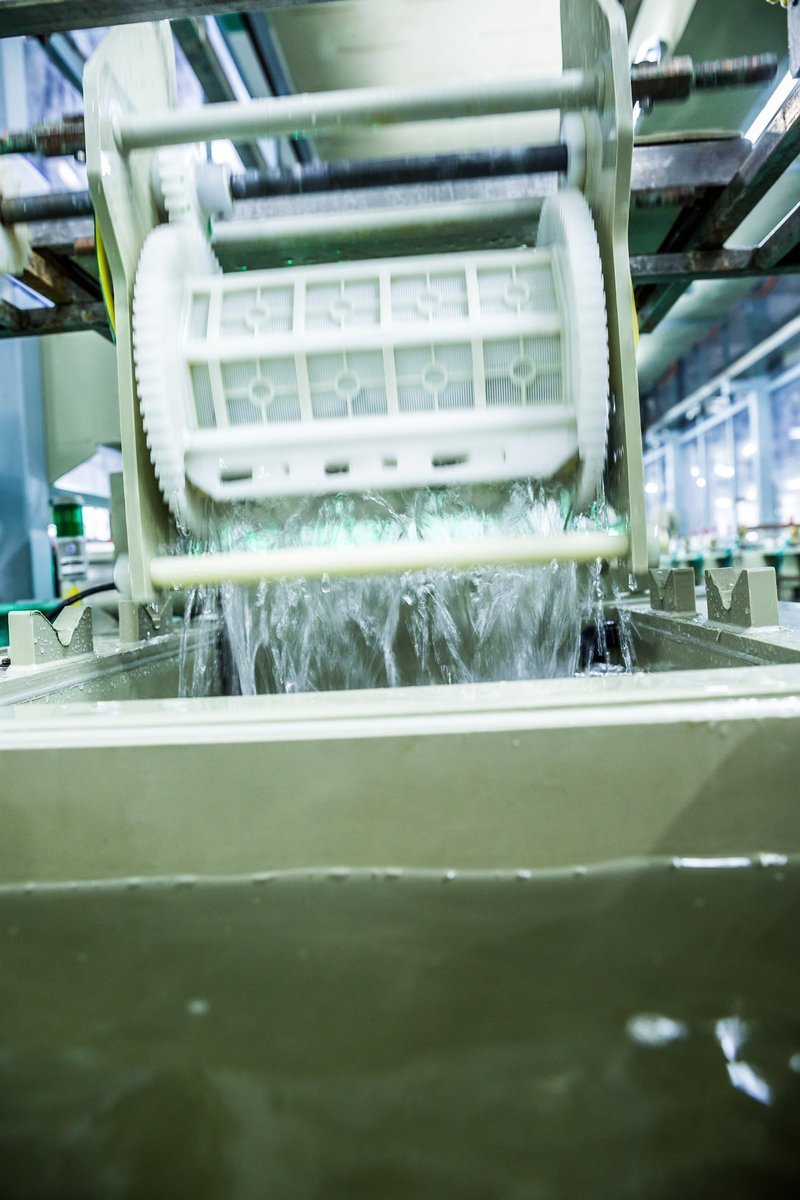
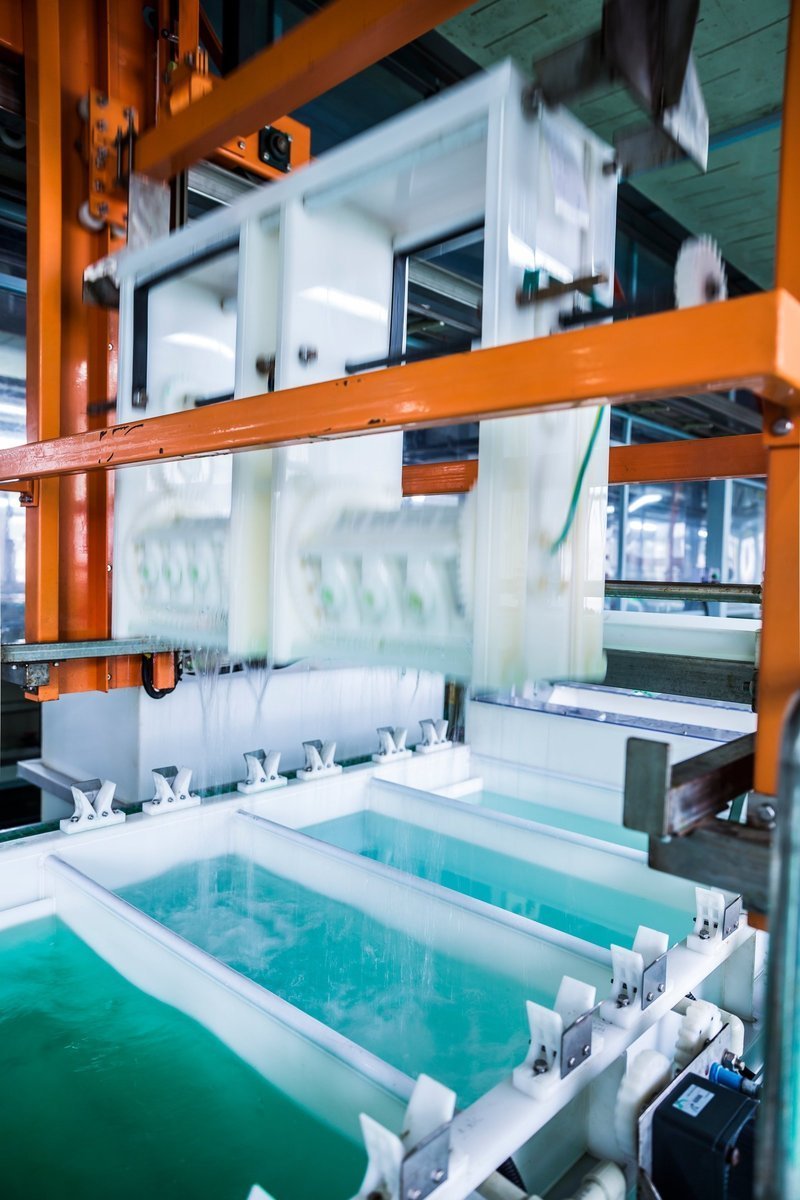
5. Performance characteristics of the special cleaning machine for neodymium-iron-boron magnetic materials
Due to the large batch size, long process, harsh environment of electroplating workshop, harsh production conditions and other factors for the cleaning of Nd-Fe-B magnetic materials, the performance requirements of ultrasonic cleaning equipment are different from those used in the general machining industry. The technical difficulties are:
(1) The load changes greatly. Due to the manual operation of the cleaning process, the number of workpieces placed in the tank, the water level, and human factors are more random, and the load changes are often large. This requires the ultrasonic cleaning equipment to work stably under variable loads, and the cleaning capacity should not change too much.
(2) The cleaning tank is shallow. The shallow cleaning tank is convenient for cleaning operations, but the low liquid level often makes the ultrasonic equipment run at a high power. Individual operators often keep the power off when draining the liquid, which makes the equipment run without liquid in a short period of time, resulting in excessive amplitude of the steel plate in the cleaning tank, and the internal stress exceeds the fatigue strength of the material, resulting in micro-cracks inside the steel plate. This kind of micro-cracks Once generated, under the action of ultrasonic vibration, the crack will gradually expand and cause the steel plate to crack. To avoid this situation requires special measures in the structural design of the equipment.
(3) The acid mist atmosphere and humid environment in the electroplating workshop have a great impact on the equipment. Acid mist and humidity can easily corrode and short-circuit the electronic components of ultrasonic equipment.
In order to adapt to the cleaning method and working conditions of neodymium-iron-boron magnetic materials, this puts forward more stringent requirements on the structural design, material selection and manufacturing process of ultrasonic cleaning equipment.