NdFeB magnet common plating introduction
NdFeB magnet common plating introduction
Nickel Plated Coatings
Nickel plated magnets and the most common coating on most magnets on the market. This coating is usually used as a triple coating (nickel-copper-nickel) with copper in the middle. It is ideal for indoor/outdoor use as long as it is moisture resistant.
The nickel coating is also available as black nickel with a shiny dark gray/charcoal color.
Electroless nickel coating
Chemical nickel plating is similar to regular nickel plating, except that it is almost completely resistant to alkalis, salt/brine solutions, chemical and petroleum environments and all types of hydrocarbons, solvents, ammonia solutions and acids. This makes chemical nickel plating an excellent choice for magnets that require corrosion resistance.
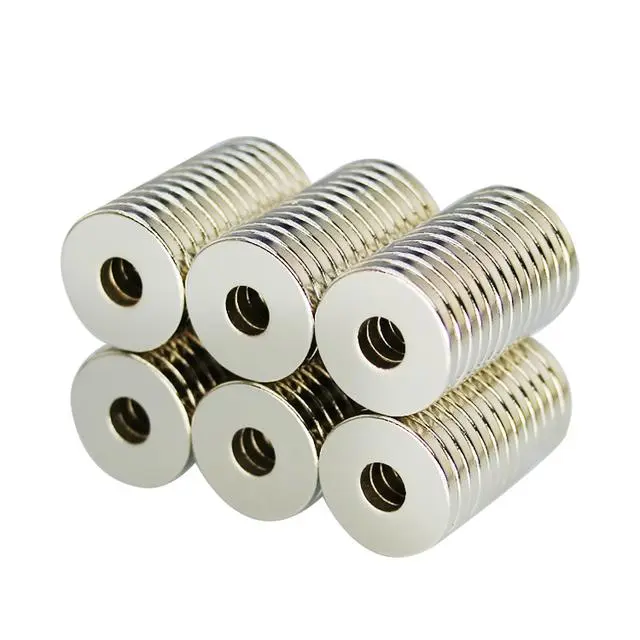
Zinc Plated Coatings
Zinc is commonly used as a single layer coating. It offers excellent performance as a corrosion resistant coating and is economically priced. As the zinc begins to oxidize, it forms a layer of zinc oxide that helps protect the magnet.
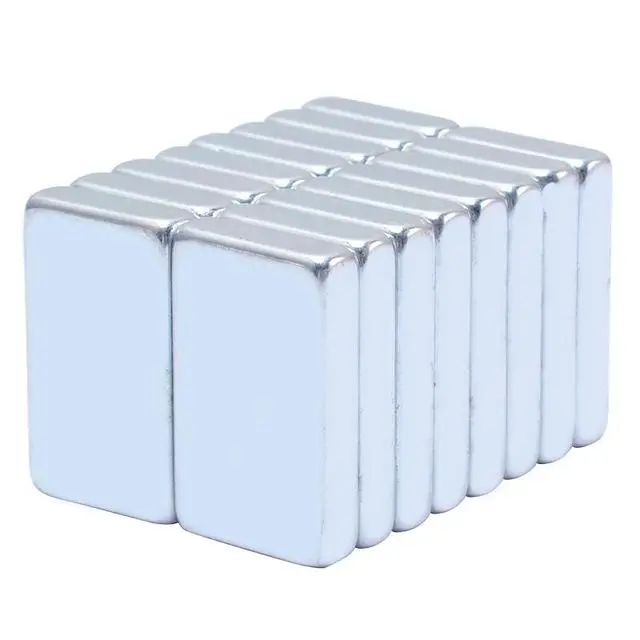
Epoxy Coating
The epoxy coating is mostly black in color and is covered with a triple nickel coating (Ni-Cu-Ni-Epoxy). It provides excellent performance in outdoor applications where corrosion resistance is required. This coating is softer than other coatings and scratches easily, which can expose the underlying layers and lead to magnet corrosion. Epoxy coatings are available in a variety of colors.
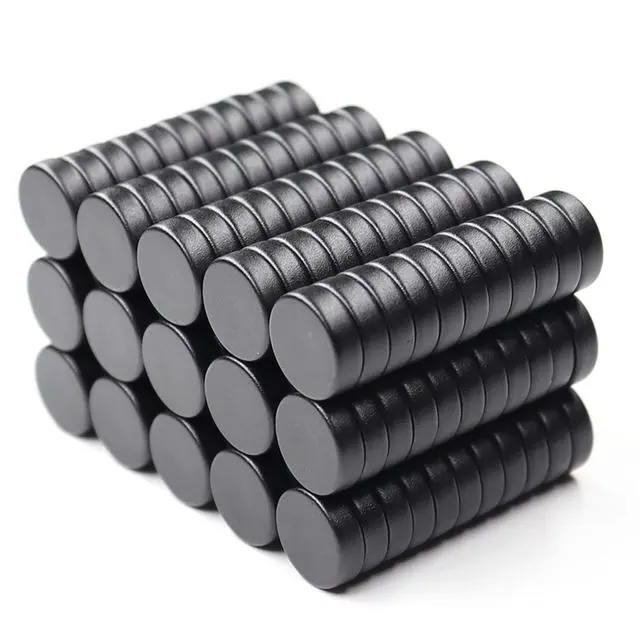
Gold Plated Coatings
Gold coatings can be used as a very thin layer of 24k gold over a nickel coating. Gold plated magnets can be gold dyed if you want to keep the cost low, but the color is not as bright as real gold. This type of coating is usually found in magnetic therapy applications.
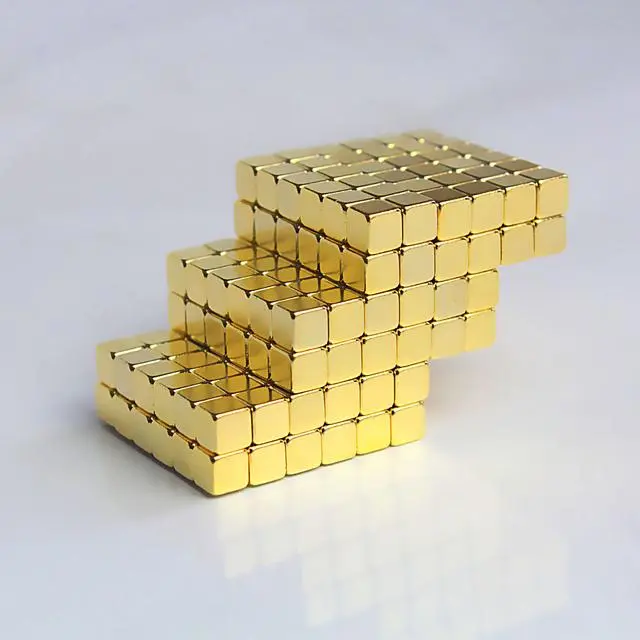
Silver Plated Coatings
Silver plating is popular in medical applications. Silver plating exhibits good corrosion resistance, biocompatibility and inherent anti-bacterial properties.
Plastic, rubber coatings
Plastic coating is super durable and highly resistant to corrosion. It protects the magnet from impact by creating a water-resistant barrier between the magnet and the component.
It prevents the magnet from breaking due to impact and prevents corrosion. This type of coating is available in any color and is more expensive than other types of coatings because it requires the use of injection molds.
The plastic coating is mostly 1 mm thick and does reduce the performance of the magnet due to its thickness.
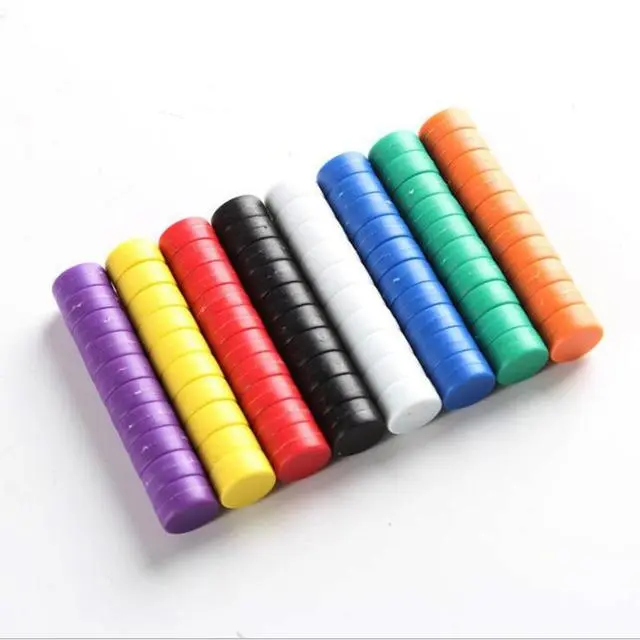
Everlube Coating
Everlube is an aluminized barrier coating that provides maximum protection against corrosion when applied to rare earth magnets. The coating is very durable and has excellent chemical and corrosion resistance to a wide range of substances.
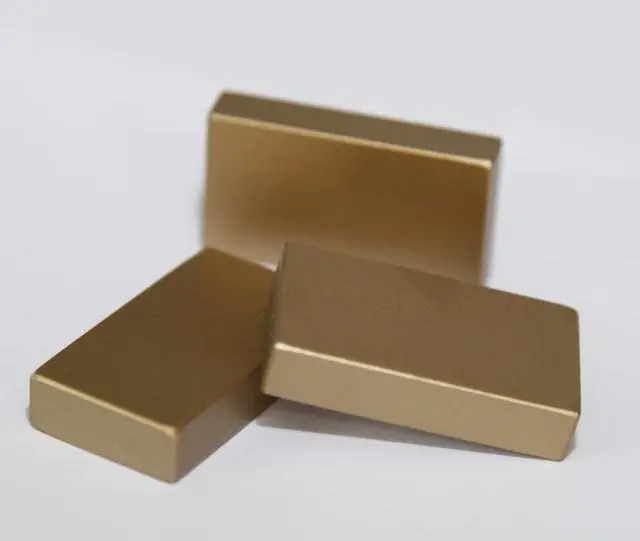
Teflon Coating
Teflon is extremely resilient and can withstand a variety of harsh environments. It has a high degree of corrosion resistance. Teflon coating does not perform well with adhesives and is therefore not recommended for these types of applications. Teflon coatings are available in a variety of colors.
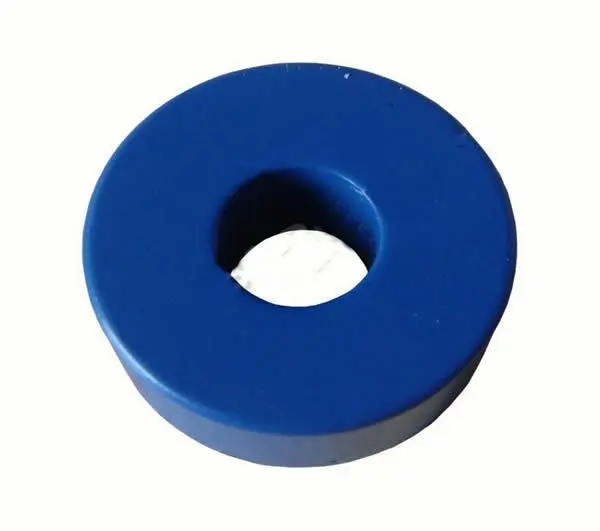
Parylene Coating
Parylene is an ultra-thin, pinhole-free polymer coating that provides excellent wear resistance and improved abrasion resistance. It is commonly used in medical devices, electronics, transportation, and defense/aerospace applications.
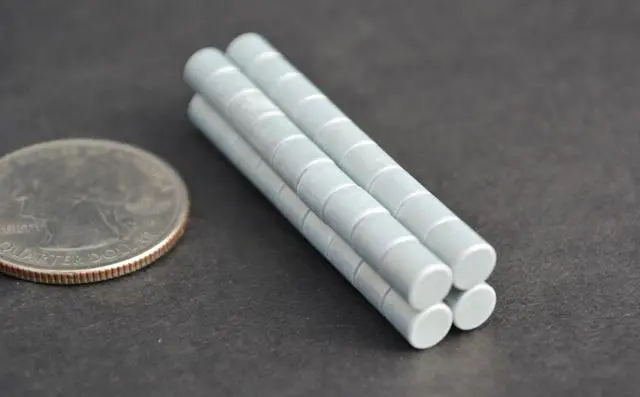