Permanent Magnet Servo Motors
A permanent magnet servomotor is a synchronous motor with feedback for commutation, velocity and position information.
Permanent-magnet motors have some performance advantages over direct-current, excited, synchronous motors, and have become predominant in fractional horsepower applications.
They are smaller, lighter, more efficient and reliable than other singly-fed electric machines.
Originally all large industrial DC motors used wound field or rotor magnets.
Permanent magnets have traditionally only been useful on small motors because it was difficult to find a material capable of retaining a high-strength field. Only recently have advances in materials technology allowed the creation of high-intensity permanent magnets, such as neodymium magnets, allowing the development of compact, high-power motors without the extra real-estate of field coils and excitation means.
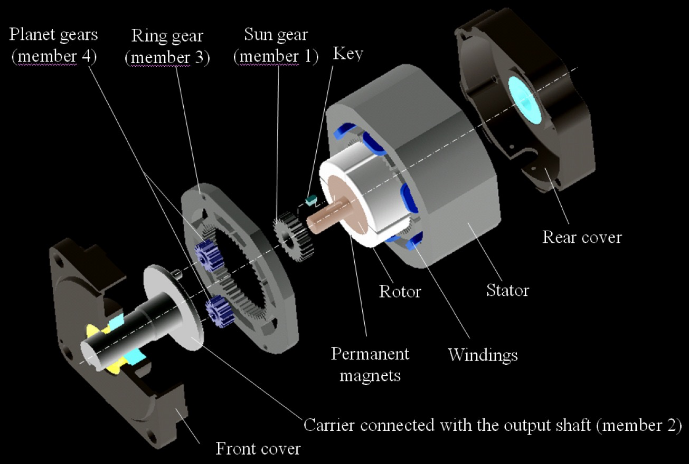
Characteristics (magnetic application):
Permanent magnet materials have been used in electric motors for decades. One important property of permanent magnets is the maximum energy product ((BH)max), which is the multiplication of residual flux density (Br) and coercive force (Hc). In other words, (BH)max represents the maximum energy available per unit volume (kJ/m3). (BH)max is also an indication of magnet force. Furthermore, the larger the (BH)max, the smaller the magnet material needed for the same force. Permeability is another important property of the magnets. It is the slope of the demagnetization curve in the linear region. Small permeability means high flux levels before the magnet is irreversibly demagnetized.
Alnico magnets can be magnetized in any direction by simply heating the magnet and cooling them in a magnetic field to give a preferred magnetic direction.
Traditionally, Alnico magnets were largely used in permanent magnet servo motors. One advantage of Alnico magnets is that they have a high residual flux density (Br). They have excellent temperature stability and strong corrosion resistance level. Their working temperatures can go up to 550 degrees. However, they can be demagnetized easily. In addition, the maximum energy product ((BH)max) of these magnets is not very high.
Ferrite magnets (ceramic magnets), have very high intrinsic coercive force (Hci) and therefore, they are very difficult to demagnetize. They can easily be magnetized in a variety of formats. The raw material is so abundant that it is found in numerous applications. This kind of magnet material has a good resistance to corrosion and can operate at high temperatures up to 300 degrees. These materials are used for permanent magnet server motor where space and cost are not important requirements.
Rare-earth magnets are strong permanent magnets made from the alloys elements such as Neodymium and Samarium. Discovery of these strong magnets have changed the future of permanent magnet motor technology as well as servo motors and the magnetic field can be increased to 1.5T levels.
The first generation rare earth magnets use Samarium and Cobalt (SmCo). One of the biggest advantages of such magnets is that they provide very high maximum energy product ((BH)max) compared to Alnicos and Ferrites. This big improvement in high maximum energy product ((BH)max) is made possible by the high coercive force (Hc). Nonetheless, they are very brittle and both the raw material cost and the production cost are relatively higher than previous 2 types of magnets. Neodymium Iron-Boron (NdFeB) are produced by pressing powders in a magnetic field and their energy products can go up to 440 kJ/m3. This material is stronger than Samarium Cobalt magnets (SmCo) and the cost is relatively lower. However, NdFeB magnets have to be protected against corrosion and exposure to air/liquid and their working temperature is also lower compared to SmCo magnets.
A brief comparison of different magnets used in PM motors is illustrated in the table below. The rare earth magnets are the most common magnet materials used in PM servomotors and the table clearly shows significant benefits of such magnets. NdFeB magnets have higher flux density levels up to 1.5T and higher MEPs but their working temperature is lower (up to 200 oC).
Table 4. Typical permanent magnet material magnetic properties
Materials | Br [T] | Hc [kA/m] | (BH)max [kJ/m³] | TC [℃] | Tw-max [℃] |
Alnico | 1.4 | 120 | 96 | 850 | 550 |
Ferrite | 0.46 | 354 | 42 | 450 | 250 |
SmCo | 1.2 | 800 | 255 | 820 | 350 |
NdFeB | 1.5 | 910 | 440 | 380 | 220 |
*All values in the table are maximum figures
Testing: (permanent magnet servo motor as an example)
Magnetic property:
A.Demagnetization curves in room temperature and designated high temperature
Supporting Equipment: Hysteresisgraph
Applicable magnet types: NdFeB magnets, SmCo magnets, hard ferrites, AlNiCo magnets
B.Irreversible demagnetization by comparing
1.Magnetic flux in room temperature
2.Magnetic flux after magnets are heated in elevated temperature
Important: The consistency of the flux is critical and matters even more after they are mounted on the stator surface. Vector Magnets possesses strict control of flux test for motor magnets so as to ensure the motor would obtain the best possible performance.
Supporting Equipment: flux meter, industrial oven
Applicable magnet types: NdFeB magnets, SmCo magnets, hard ferrite magnets.
Appearance and dimensions
A.Appearance:
Salt Spray Test: set in certain humidity, PH based on application
Press Cook Test: set in air pressure, temperature and humidity based on application.
Plating/Coating thickness; using x-ray-fluorescence to analyze the thickness of surface plating/coating.
Supporting Equipment: Salt Spray Cabinet; Press Cook Test cbinet; XRF analyzer,
Applicable magnet types: NdFeB magnets, SmCo magnets
B.Metal Flaw (crack) Detection
C.Dimensions:
1.Geometric tolerances (critical features, e.g. parallelism, perpendicularity, etc)
2.Desired size and shape
Supporting Equipment: micrometer, caliper, image measurement tool, CMM (Coordinate Measurement Machine)
Applicable magnet types: NdFeB, SmCo, hard ferrite magnets, AlNiCo magnets